Cylinder Repair
Process Pump & Seal is not only a distributor of Chesterton hydraulic and pneumatic sealing kits and solutions, but is also able to repair and upgrade your current cylinders. We make sure that all dimensions, clearances and surface finishes meet or exceed OEM specifications.
Our Dissasembly Process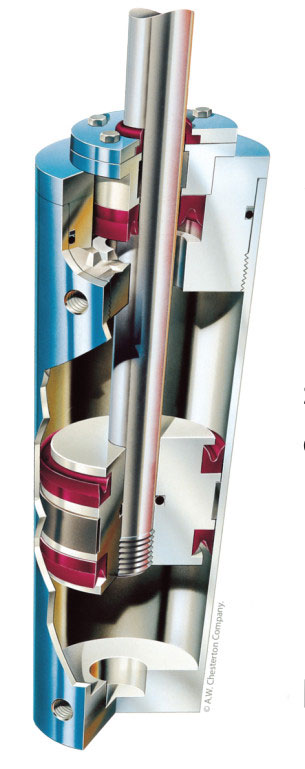
- Mark cylinder and all components, identifying port/cap orientations
- Disassemble / clean all cylinder components
- Visually inspect all components for wear, sealing device condition and note probable cause of failure
We Record and Measure all Cylinder Components
- Rod diameter
- Rod straightness
- Piston diameter
- Inside tube diameter
- Inside gland diameter
- Piston groove inside diameters and width
- Gland seal and wiper groove diameters and width
- Tube end seal (and all static seal) groove width & depth
- Check and record rod and piston surface finishes
- We provide report of our findings to you to help your team make the best go-forward descision
We Upgrade Materials and Processes For Extended Cylinder Life
- Utilize thermostat polyurethanes offering high abrasion and cut resistance, low compression set, self-lubricating rod/piston seals, wipers, tube seals
- Install replaceable high compressive strength wear rigns on piston and gland wear surfaces where applicable
- Apply aluminum bronze overlay on piston where applicable
- Rods to be chrome plated or HVOF coated and ground black to proper diametrical clearances
Assembly Procedure
- Hone cylinder bore to restore proper surface finish
- Polish piston rod as needed to restore proper surface finish
- Assemble all sealing devices and components using proper lubrication
- Torque all fasteners per OEM specifications using proper lubrication
- Perform cylinder testing using hydraulic oil (or air on pneumatics) checking for proper extension and retraction
- Confirm that internal and external leakage control meets or exceeds OEM specifications
- Surface prep and paint cylinder. Install protective plugs on ports and wrap exposed rod end